Computer Panel Beam Saw is crafted for skilled carpenters and construction workers who need accuracy in cuts and tools instead of merely cutting down large boards or other lumber.
By cutting the material with a computer panel saw, you can significantly reduce material or lumber waste. This is why many woodworkers employ this type of saw in their projects.
If you want to learn more about the features of a Computer Panel Beam Saw and how it can help woodworkers, you should continue reading the article for a better understanding.
Short Overview of Computer Panel Beam Saw
A computer panel saw is a type of construction saw used in the building and carpentry industries. The computer panel saw is intended to cut large sheets of plywood, plastic, and other materials.
It is highly versatile and can be employed to cut varied types of materials, including aluminum, PC panels, and more.
The main intention of a computer panel saw is to slash large pieces of wood into thin boards. This authorizes you to build different types of wood products, including flooring, wall paneling, and furniture.
It allows the carpenter to get a detailed measurement of how much they need to cut off from their materials before they start using them.
The saw is also faster and safer than traditional saws as there is less risk of dangerous accidents such as kickback.
Features of Computer Panel Beam Saw
1. High Precision
The computer panel saw machine has an incredibly high cutting precision and high-speed cutting function, making the cutting shape smoother and more precise.
This ensures better edge sealing and foil effect.
1. Keep workers Safe from Injury
Automatic panel saws are safer than manual ones. The risk of employees getting injured reduces, and they can work skillfully.
2. Less Surface Damage
The floating effect of the floating platform is generated by the pressure, making it easier to feed large plates and avoiding damage to the surface.
3. Imported Magnetic Feet are Used
The computer panel saw machine uses imported magnetic feet as feed positioning detection control.
This allows for exact positioning detection size effectively, hence improving the cutting precision.
4. High-Quality CPU is Used
The computer panel saw machine makes use of a Japanese Mitsubishi CPU control board of the highest grade.
5. Advanced Electrical Control Design is Used
The safety and efficiency of processing are assured through the use of equipment with an advanced and suitable electrical control design that is capable of automated return.
6. An automatic Sheet-feeder is Used
The computer panel saw machine uses an automatic sheet-feeder equipped with a high-performance servo motor drive manufactured by Mitsubishi in Japan.
This offers a large torque, accurate placement, and long service life.
Benefits of Using Computer Panel Beam Saw
Some benefits of using computer panel beam saw are given as under:
1. High-Quality Cut
The computer panel saw is not only safe and silent but also produces a high-quality cut.
2. Boosts Efficiency
It won't need a lot of manual labor from you, but it can significantly boost the efficiency of your manufacturing.
3. Adjust its Speed Based on the Material
Computer Panel Beam Saw has the capability to automatically alter its cutting speed in response to the nature of the material they are cutting through.
4. Continuous Working of Saw Blade
The saw blade moves continuously because of the smart control system.
5. Automate Trimming and Stacking
Computer Panel Beam Saw is able to stack and trim materials automatically.
6. High Stability
The use of electrical components from international brands ensures a high level of stability.
7. Safety Shield
Protecting operators from flying sawdust and noise while isolating them from the source of the noise is possible with a safety shield that is completely sealed.
Classification of Computer Panel Beam Saw
Based on structural design, panel saws are classified into:
· Horizontal
· Vertical
Horizontal
The horizontal panel saw is designed for cutting material that is wider than it is tall (like sheet metal).
They are generally big table saws equipped with a sliding feed table that propels the material through the saw's blade.
The immediate advantage of this type of saw is that it can be used to cut large sheets of material quickly and easily. It has less flexibility than a vertical panel saw, but it's also easier to use.
Vertical
The vertical panel saw is designed to cut material that is taller than it is wide (like plywood). In a vertical panel saw, the blade's path remains fixed as the workpiece is moved along it.
In addition to cutting plywood, these saws can be used when installing cabinets or building furniture.
They can also be classified according to the mode of operation they use, which can be:
· Computer Numerical Control (CNC)
· Manual Control
CNC
Using a CNC panel saw machine is safe since the machine is controlled by a computer and regulated by frequency and speed, so there is no need to slide the material manually.
It can process wood and other types of materials such as metals.
Manual Control
When using manual panel saws, the operator must direct the sawing mechanism as it cuts through the workpiece.
When using a manual panel saw, employees, are at risk of injuring their fingers or hands.
It can process wood only.
Types of Wood that Computer Panel Beam Saw can Process
You may work with various types of wood and want to know what types of wood that wood saw machine can process.
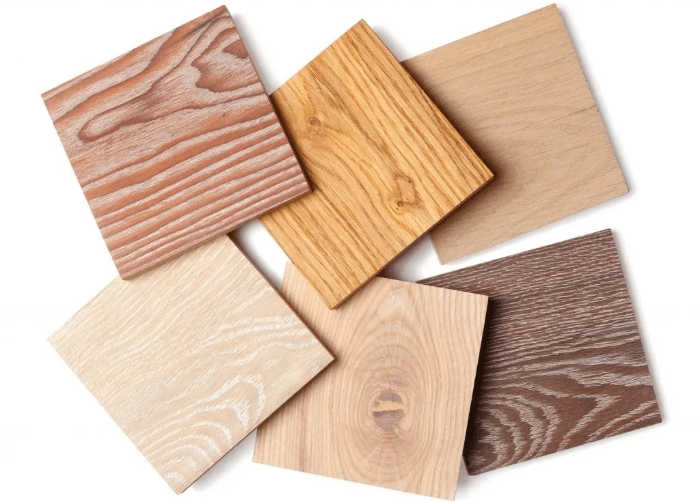
Wood saw machines are designed for explicit types of wood and cutting applications. The type of wood you plan to cut will determine which type of machine is best for your job.
· Plywood
· Particleboard
· MDF
In addition to these types of woods, other types of woods can be cut using a wood saw machine.
· PS panels
· PC panels
· MMPA
Conclusion
Thanks to the computer panel saw, carpenters and construction workers of all kinds can work safely and efficiently.
This technological innovation frees up a great deal of time and energy while simultaneously making it safer for everyone involved to get the job done. It is a perfect tool for projects dealing with precision materials.